Competition Highlights Hot Features. The Copeland® System Pro™ is a fractional horsepower condensing unit that reduces the amount of necessary on-site installation supplies, tube prepping, and brazing, and provides a solution to working in restricted places. The unit comes with factory-installed, -sealed, and -tested system protection devices already in place.
[More]
The Hermetic Moisture Indicator (HMI) from Flow Controls, Division of Emerson Climate Technologies (St. Louis), earned the bronze award. The comment from one contractor-judge was simply, “This is a real improvement over the competition.”
Emerson Climate Technologies said its Hermetic Moisture Indicator is designed to alert technicians to moisture levels lower than 3 percent relative humidity.
[More]
We are an Authorized distributor for Emerson Climate Technologies Flow Controls. Formerly Alco Controls.
Wednesday, December 31, 2008
Tuesday, December 16, 2008
Monday, November 24, 2008
Take-A-Part Thermo Expansion Valves

Power assembly, cage assembly and flange. There are no working parts in the flange. It is never necessary to break the line connections to service the valve.
Sunday, November 23, 2008
Acid Test Kit

The universal acid test kit provides a reliable indication as to the acid level of the refrigeration oil. It is quick and easy! They are for use with all refrigeration lubricants. By changing the percentage of oil sample taken, the acid number of the oil can be accurately determined. Phase separation of the chemicals eliminates interference from discoloured oil.
Tuesday, November 11, 2008
Water Dump Valve for Ice Machines

Ice machines operate like no other type of refrigeration equipment. The application challenge posed by the duty cycle of an ice machine is to balance efficient, productive ice making with reliable operation, low sound and cost. Operators count on their ice machines to provide quantities of ice year-round, and they count on their refrigeration contractor to keep them running at peak efficiency. Whether it's a new installation, field replacement or retrofit, the right water dump valve is essential for reliable, productive ice making.
Tuesday, September 30, 2008
Factory Set Superheat
Our thermostatic expansion valves are factory set to a specific superheat. If adjustment is needed, refer to superheat adjustment instructions for proper procedure. Kindly check with your local Emerson Flow Controls wholesale specialists for step-by-step guide.
Improper adjustment may result in valve malfunction and /or system damage.
Saturday, September 27, 2008
Measuring Superheat
Where possible, always select a thermal expansion valve for the actual operating conditions rather than nominal valve capacities.
To determine the valve is working properly is by measuring its superheat.
The degree to which the refrigerant gas is superheated depends on
1) the amount of refrigerant being fed to the evaporator by the valve
2) the heat load to which the evaporator is exposed.
Thursday, September 25, 2008
Service Instructions for Take-A-Part Thermo Expansion Valves
Before opening any system, make sure the pressure in the system is brought to and remains at atmospheric pressure. Failure to comply may result in system damage and /or personal injury.
To inspect, clean, or replace parts of the Thermo valve:-
1) Disconnect equalizer line
2) Remove cap screws
3) Carefully lift off the power assembly
4) Remove cage assembly and gaskets
5) Lightly oil gasket with refrigeration oil
Best practice: Replace all gaskets whenever a valve is opened.
6) Assemble in the same order as disassembled
7) When putting the power assembly on, make sure the cage assembly lugs line up with the slots inside the power assembly
8) Tighten cap screws evenly and torque to 300 inch pounds
9) Check for leaks
To inspect, clean, or replace parts of the Thermo valve:-
1) Disconnect equalizer line
2) Remove cap screws
3) Carefully lift off the power assembly
4) Remove cage assembly and gaskets
5) Lightly oil gasket with refrigeration oil
Best practice: Replace all gaskets whenever a valve is opened.
6) Assemble in the same order as disassembled
7) When putting the power assembly on, make sure the cage assembly lugs line up with the slots inside the power assembly
8) Tighten cap screws evenly and torque to 300 inch pounds
9) Check for leaks
Wednesday, September 24, 2008
Superior filtration for greater refrigeration protection
The Extra Klean EK Filter Drier
Get a bead on superior contaminant protection
When it comes to the refrigeration systems you install and maintain, what matters most? It is keeping them running at peak efficiency. Keeping your reputation intact and your customers satisfied. It is choosing superior filtration technology that delivers more reliable, longer-lasting protection from moisture and contaminants.
The EK Filter Drier offers unprecedented operational flexibility. It’s an ideal solution whether you’re using HCFCs, CFCs or newer HFC refrigerants. In fact, the EK Filter Drier is Copeland recommended for HFCs such as R-410A. Its beaded desiccants protect new POE oils from contaminants and quickly absorb and remove any moisture before acids can form. And there are a variety of available models to meet any system demand.
More information here.
Get a bead on superior contaminant protection
When it comes to the refrigeration systems you install and maintain, what matters most? It is keeping them running at peak efficiency. Keeping your reputation intact and your customers satisfied. It is choosing superior filtration technology that delivers more reliable, longer-lasting protection from moisture and contaminants.
The EK Filter Drier offers unprecedented operational flexibility. It’s an ideal solution whether you’re using HCFCs, CFCs or newer HFC refrigerants. In fact, the EK Filter Drier is Copeland recommended for HFCs such as R-410A. Its beaded desiccants protect new POE oils from contaminants and quickly absorb and remove any moisture before acids can form. And there are a variety of available models to meet any system demand.
More information here.
Monday, September 22, 2008
Thursday, September 18, 2008
Oil level monitoring controls
Maintaining proper oil level is of primary importance for a long compressor lifetime. Especially when paralleling compressors in compressor pack applications, maintaining sufficient oil in the compressor’s crankcase becomes difficult. A simple way of balancing the oil level in parallel compressor arrangements is the use of oil equilibrium lines. These systems are also referred to as passive systems. However, passive systems require individual tailoring for each application and they only perform satisfactorily under more or less constant operating conditions. Particularly in refrigeration applications with varying operating conditions and defrost cycles an active means of oil level management is a must in order to ensure reliable compressor operation. An additional benefit of active systems is that, apart from oil balancing, they normally also monitor the oil level and provide alarming capabilities. This is a particular benefit for scroll compressors which, due to the lack of an integral oil pump, do not have a differential oil pressure switch as conventional compressors have. The OMB is a self-contained system which provides both functions, oil level monitoring and oil level balancing, for active oil level management systems. The OMB system is applicable to low and high pressure oil management systems. Traditional oil level management systems work with a low pressure oil reservoir. The oil is kept at a pressure slightly above suction pressure by a differential pressure valve.
Look here for high efficiency oil separators for your systems.
Tuesday, September 16, 2008
Specify the Emerson oil controls solution.
When it comes to managing refrigeration systems, one of the main concerns is to keep the compressor lubricated while maintaining a high level of heat transfer and energy efficiency by removing as much oil as possible from the refrigerant. This requires sophisticated oil management devices. Emerson Climate Technologies offers a complete range of premium quality mechanical and electronic oil control devices aimed at keeping your refrigeration systems at peak performance at all times. A-WC/A-FC series centrifugal oil separators feature higher oil removal efficiency and lower pressure drop than the leading competition, according to independent test lab results. The OMB electronic oil level control employs Reverse Hall Effect sensing technology to precisely determine the compressor crankcase oil level and feed oil exactly when needed. Its five times lockout feature provides extra protection to the compressor. Specify Emerson again & again! Install confidence everytime and for every jobs!
Friday, September 12, 2008
Specify the Emerson system protectors solution.
When it comes to the refrigeration systems you install and maintain, what matters the most? It’s keeping them running at peak effi ciency. Keeping your reputation intact and your customers satisfi ed. It’s the kind of protection you can only get from the established industry leader, Emerson Climate Technologies. Our EK filter driers, HMI hermetic moisture indicators, along with many other high performance products, provide you with a total package that delivers more reliable and longer lasting protection from moisture and contaminants. Come see for yourself what the total package is all about. Specify Emerson for every jobs! Install Confidence!
Thursday, September 11, 2008
What makes Emerson’s moisture indicator better? Early detection
The 3% difference.
What makes Emerson’s moisture indicator better? Early detection. The HMI’s patented wafer dial uses a three-step gauge to detect moisture at 3% relative humidity (RH) – giving you plenty of time to make necessary adjustments before any damage is done. Ordinary indicators use a two-step paper gauge that only detects moisture at 10% RH – a level that is more than enough for corrosive acids to build up and totally destroy a system.
Designed for today. Made for tomorrow.
The added moisture sensitivity of the HMI makes it ideal for nearly every refrigerant available – from HCFCs to new higher-pressure HFCs (including R-410A). In fact, the HMI is available with both ODF and SAE connections and is the only moisture indicator UL-approved to 680 psig. So even as your customers’ systems undergo mandated changes in the next few years, the HMI you install today will work with the refrigerants of tomorrow.
Built to last with a universal fit.
The HMI has an airtight, corrosion-resistant brass body with no o-rings or knife-edge seals for guaranteed leak-free operation. Plus it is heat resistant, so you can braze without having to worry about damaging the internal wafer dial. For installation, the HMI features solid copper fittings for easy, universal replacement of any brand indicator. Saving you time, along with your reputation.
Now you see it. Now you know.
Let’s face it, moisture indicators are almost always in dark areas with poor light. Which is why we gave the HMI a wide-angle, .71 square-inch viewing lens – by far the biggest in the industry. And with an easy-to-read tri-color-coded system, you’ll be able to read the dial even in low light.
Paper or plastic?
The HMI wafer dial is a molded disk that is significantly more durable than ordinary paper indicators. And it is more sensitive to lower levels of moisture (3% versus 10% relative humidity). In fact, the color in a paper indicator can actually wash out under wet conditions. Plus paper indicators are highly susceptible to damage from brazing during installation.
Protect your reputation with the HVAC/R technology leader.
When it comes to your HVAC/R systems, you have enough things to worry about. Your reputation shouldn’t be one of them. With Emerson’s HMI, you know your customers are getting a better indicator and you are getting a better warning system. After all, your reputation is worth it.
Lets look at the review from http://www.achrnews.com.
Earlier indication.
Better design. More reliability. The Emerson Climate Technologies Hermetic Moisture Indicator. Buy yours from our selected wholesalers.
What makes Emerson’s moisture indicator better? Early detection. The HMI’s patented wafer dial uses a three-step gauge to detect moisture at 3% relative humidity (RH) – giving you plenty of time to make necessary adjustments before any damage is done. Ordinary indicators use a two-step paper gauge that only detects moisture at 10% RH – a level that is more than enough for corrosive acids to build up and totally destroy a system.
Designed for today. Made for tomorrow.
The added moisture sensitivity of the HMI makes it ideal for nearly every refrigerant available – from HCFCs to new higher-pressure HFCs (including R-410A). In fact, the HMI is available with both ODF and SAE connections and is the only moisture indicator UL-approved to 680 psig. So even as your customers’ systems undergo mandated changes in the next few years, the HMI you install today will work with the refrigerants of tomorrow.
Built to last with a universal fit.
The HMI has an airtight, corrosion-resistant brass body with no o-rings or knife-edge seals for guaranteed leak-free operation. Plus it is heat resistant, so you can braze without having to worry about damaging the internal wafer dial. For installation, the HMI features solid copper fittings for easy, universal replacement of any brand indicator. Saving you time, along with your reputation.
Now you see it. Now you know.
Let’s face it, moisture indicators are almost always in dark areas with poor light. Which is why we gave the HMI a wide-angle, .71 square-inch viewing lens – by far the biggest in the industry. And with an easy-to-read tri-color-coded system, you’ll be able to read the dial even in low light.
Paper or plastic?
The HMI wafer dial is a molded disk that is significantly more durable than ordinary paper indicators. And it is more sensitive to lower levels of moisture (3% versus 10% relative humidity). In fact, the color in a paper indicator can actually wash out under wet conditions. Plus paper indicators are highly susceptible to damage from brazing during installation.
Protect your reputation with the HVAC/R technology leader.
When it comes to your HVAC/R systems, you have enough things to worry about. Your reputation shouldn’t be one of them. With Emerson’s HMI, you know your customers are getting a better indicator and you are getting a better warning system. After all, your reputation is worth it.
Lets look at the review from http://www.achrnews.com.
Earlier indication.
Better design. More reliability. The Emerson Climate Technologies Hermetic Moisture Indicator. Buy yours from our selected wholesalers.
Tuesday, September 09, 2008
HFC Refigerants and POE Lubricants - Part 3: How to combat water in the system [2]?
Another aspect of POE oil is the ability to keep more solid particles in suspension than Mineral oil. This is particularly important in retrofitted systems where pockets of solid contamination are now flushed from low flow areas and need to be removed before moving parts in the system are damaged. The filter-drier for POE oils needs to have increased solid particle holding capacity with minimal impact to refrigerant flow capacity or pressure drop.
The filter-drier should also have improved contaminate removal efficiency as well to ensure that all particles are captured the first time they enter the filter-drier. The ability to remove smaller particles is also advantageous. The EK series filter-driers provide a unique combination of these characteristics to provide outstanding filtration.
The filter-driers for use in HFC and POE oil systems must maintain the system dry and free of any acids that may have been generated. However, since water capacity is of primary importance the filter-drier should contain a higher percentage of molecular sieve than was required for CFC and HCFC systems. But molecular sieve alone is not sufficient since it has virtually no organic acid capacity. An organic acid removal desiccant must be used such as activated alumina to ensure low acid levels are maintained. In addition, the filter-drier should also have increased filtration capacity and efficiency.
The EK filter-driers provides the optimal combination of these properties to ensure the long, trouble free life of any air-conditioning or refrigeration system.
The moisture indicating sightglass must also indicate moisture level in the range of less than 50 ppm moisture. Also, it must be able to perform this function at the temperature of the liquid line on which it is placed. Many sightglasses cannot perform this function at all liquid line temperatures. This low level indication ability is necessary to ensure that the system moisture never exceeds the level at which organic acid formation starts. The HMI & AMI moisture indicating sightglasses provide this low level detection early.
The filter-drier should also have improved contaminate removal efficiency as well to ensure that all particles are captured the first time they enter the filter-drier. The ability to remove smaller particles is also advantageous. The EK series filter-driers provide a unique combination of these characteristics to provide outstanding filtration.
The filter-driers for use in HFC and POE oil systems must maintain the system dry and free of any acids that may have been generated. However, since water capacity is of primary importance the filter-drier should contain a higher percentage of molecular sieve than was required for CFC and HCFC systems. But molecular sieve alone is not sufficient since it has virtually no organic acid capacity. An organic acid removal desiccant must be used such as activated alumina to ensure low acid levels are maintained. In addition, the filter-drier should also have increased filtration capacity and efficiency.
The EK filter-driers provides the optimal combination of these properties to ensure the long, trouble free life of any air-conditioning or refrigeration system.
The moisture indicating sightglass must also indicate moisture level in the range of less than 50 ppm moisture. Also, it must be able to perform this function at the temperature of the liquid line on which it is placed. Many sightglasses cannot perform this function at all liquid line temperatures. This low level indication ability is necessary to ensure that the system moisture never exceeds the level at which organic acid formation starts. The HMI & AMI moisture indicating sightglasses provide this low level detection early.
Monday, September 08, 2008
HFC Refigerants and POE Lubricants - Part 2: How to combat water in the system [1]?
Refrigerant systems must be dry internally because high moisture content can cause ice to form in the expansion valve or capillary tube, corrosion of bearings, reactions that affect lubricant / refrigerant stability, or other operational problems. As with other components, the refrigeration lubricant must be as dry as practical. Polyolesters [POE] usually contains 50 to 100 ppm moisture in normal manufacturing. This amount may increase between time of shipment from the refinery and the time of actual use.
POE oils are quite hygroscopic in its properties.
Monitoring
To combat the detrimental effects of water in HFC and POE systems it is imperative to hold moisture levels as low as possible. It is generally accepted that water level must be maintained less than 50 ppm in the refrigerant and the same for the oil. Monitoring is therefore necessary. In order to monitor system water level a moisture indicator must be used that can sense changes in moisture in this ppm range.
Many commercial sightglasses cannot indicate a change at this level in liquid lines that exceed 100degF or 38degC. This means that harmful organic acids may be attacking system components while the indicator is showing 'dry'. The HMI and AMI moisture indicators have unique element that has the ability to change colour at low ppm levels so that proper action can be taken before any system components are damaged.

Filtering
Because POE lubricants are quite hygroscopic, when they are in a refrigeration system they should circulate through a filter-drier designed for liquids. A filter-drier must be installed in the line carrying liquid refrigerant or in a line returning lubricant to the compressor. The desiccants will remove some additives in the lubricants. It was necessary to redesign standard 'catch-all' filter-driers for increased water removal capacity to achieve these low moisture levels. Since no system is entirely devoid of water upon startup some organic acids will be generated and must be removed.
The desciccant formulation for the EK and UDK series of filter-driers was designed to provide the optimal mix of water capacity and acid capacity to ensure that both harmful contaminates are effectively removed. This desiccant mixture contains both molecular sieve and activated alumina. The molecular sieve is specially designed to provide maximum drying in today's systems. The activated alumina is ideal for capturing the large organic acids that the molecular sieve cannot.
POE oils are quite hygroscopic in its properties.
Monitoring
To combat the detrimental effects of water in HFC and POE systems it is imperative to hold moisture levels as low as possible. It is generally accepted that water level must be maintained less than 50 ppm in the refrigerant and the same for the oil. Monitoring is therefore necessary. In order to monitor system water level a moisture indicator must be used that can sense changes in moisture in this ppm range.
Many commercial sightglasses cannot indicate a change at this level in liquid lines that exceed 100degF or 38degC. This means that harmful organic acids may be attacking system components while the indicator is showing 'dry'. The HMI and AMI moisture indicators have unique element that has the ability to change colour at low ppm levels so that proper action can be taken before any system components are damaged.


Filtering
Because POE lubricants are quite hygroscopic, when they are in a refrigeration system they should circulate through a filter-drier designed for liquids. A filter-drier must be installed in the line carrying liquid refrigerant or in a line returning lubricant to the compressor. The desiccants will remove some additives in the lubricants. It was necessary to redesign standard 'catch-all' filter-driers for increased water removal capacity to achieve these low moisture levels. Since no system is entirely devoid of water upon startup some organic acids will be generated and must be removed.
The desciccant formulation for the EK and UDK series of filter-driers was designed to provide the optimal mix of water capacity and acid capacity to ensure that both harmful contaminates are effectively removed. This desiccant mixture contains both molecular sieve and activated alumina. The molecular sieve is specially designed to provide maximum drying in today's systems. The activated alumina is ideal for capturing the large organic acids that the molecular sieve cannot.

Friday, September 05, 2008
HFC Refigerants and POE Lubricants - Part 1 : Why is it important?
The use of HFC refrigerants and Polyester [POE] lubricants for air-conditioning and refrigeration have generated new system chemistry related problems. New and redesigned system protectors have been developed to counteract these problems and provide a long, reliable life for the operating refrigeration system.
Moisture is the major problem causing contaminate for HFC/POE oil systems just as was for CFC and HCFC systems using Mineral oil. Many HFC's can hold much more water than their CFC counterparts but the oil differences are much worse than those of the refrigerant. POE oil can hold as much as 10 times more water than Mineral oils. In addition, evacuation has proven ineffective at removing this moisture so as a filter-drier is required to perform this function.



Water poses a new problem for POE oils above and beyond those experienced with Mineral oil. POE oil will react with water to form organic acids at normal operating conditions in refrigerating and air-conditioning systems. This reaction starts at water levels as low as 75ppm. These acids attack system components including motor insulation and metallic components --- reducing system life.
Moisture is the major problem causing contaminate for HFC/POE oil systems just as was for CFC and HCFC systems using Mineral oil. Many HFC's can hold much more water than their CFC counterparts but the oil differences are much worse than those of the refrigerant. POE oil can hold as much as 10 times more water than Mineral oils. In addition, evacuation has proven ineffective at removing this moisture so as a filter-drier is required to perform this function.
Water poses a new problem for POE oils above and beyond those experienced with Mineral oil. POE oil will react with water to form organic acids at normal operating conditions in refrigerating and air-conditioning systems. This reaction starts at water levels as low as 75ppm. These acids attack system components including motor insulation and metallic components --- reducing system life.
Thursday, September 04, 2008
Advantages of EX Series Electrical Control Valves
The electrical control valves EX4, EX5, EX6, EX7 and EX8 from Emerson are optimized for control of liquid or gaseous mass flow in refrigeration systems. The stepper motor drive, which produces exact valve opening, is energized directly from the electrical power and therefore operates independently from differential pressure.

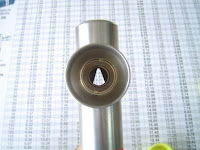
EX series electric control valves can operate from 2kW to 880kW (For R22).
EX series electric control valves can operate from 2kW to 880kW (For R22).
Wednesday, September 03, 2008
Viewing lens / HMI moisture indicator
Moisture indicators on refrigeration equipment are critical early-warning components in the effort to lessen the long-term effects of water damage and reduce repair and maintenance costs. The proper moisture indicator must sense and report just how much water is in the system’s circulating refrigerant. An indicator in a viewing lens changes color as the moisture content reaches potentially damaging levels. Be sure to choose an indicator that is sensitive enough to alert operators early on that moisture levels are rising, allowing corrective action to be taken before serious system damage occurs. The Hermetic Moisture Indicators (HMIs) from Emerson are able to read moisture levels far below industry standards. The HMI actually begins to change color at two percent relative humidity (RH), which is a “very dry” indication. At 3% RH, the purple caution color begins to appear. Many other indicators do not begin changing colors until about seven to eight percent RH; however, early detection is critical with HFC refrigerants and POE lubricants. POE oil can hold up to 20 times more moisture than the mineral oil used by older refrigerants, which can allow corrosive acids to build up and totally destroy a system. The HMI is UL listed with a 680 psig maximum working pressure, making it acceptable for use with higher-pressure HFC refrigerants. It has a larger viewing window for easier visibility and charging. It is resistant to “washout” from water and can withstand brazing temperatures up to 450 degrees Fahrenheit [ 232 degree C]. The fully hermetic design includes a corrosion-resistant, all-brass body with no o-rings or knife seals that are likely to leak. The indicator features solid copper fittings for easy, universal replacement.
Lets look at the review from http://www.achrnews.com.
Sunday, August 10, 2008
Simple guidelines for EK filter driers with refrigeration plants and air conditioning
Why use filter driers?
A refrigeration plant’s trouble-free life time is increased by:
– Moisture adsorption
– Dirt filtration
– Acid adsorption
When should I use filter driers?
As closed systems were once open and will be re-opened occasionally, filter driers will be of benefit in:
– Factory-made units
– Plants serviced or erected in the field
How and where should I use filter driers?
– Change the filter drier every time the system has been opened for service
– Mount/install a correctly sized filter drier in the liquid line after the receiver but before moisture indicators
A refrigeration plant’s trouble-free life time is increased by:
– Moisture adsorption
– Dirt filtration
– Acid adsorption
When should I use filter driers?
As closed systems were once open and will be re-opened occasionally, filter driers will be of benefit in:
– Factory-made units
– Plants serviced or erected in the field
How and where should I use filter driers?
– Change the filter drier every time the system has been opened for service
– Mount/install a correctly sized filter drier in the liquid line after the receiver but before moisture indicators
Saturday, July 19, 2008
Superheat Control with EC3-X Controllers
The pressure and the temperature of the refrigerant at the evaporator outlet are used as input signals. The controller calculates the opening of the electrical control valve [ECV] and generates the signal to drive the stepper motor. In the case of power loss, the electrical control valve is closed to protect the compressor from being flooded. To do this, a rechargeable Lead-Gel battery is built into the controller. An additional solenoid valve is no longer necessary. The refrigerant request signak us fed into the EC3-X controller through a digital input. This input is also used for temperature control and valve control.
Friday, July 18, 2008
EX4, EX5, EX6, EX7, EX8 Series Electrical Control Valves [ECV]

Thursday, July 17, 2008
Driving Directions To Our Location
FROM TUAS
1. Head northwest on Jalan Ahmad Ibrahim toward Tuas West Rd 0.2 km
2. Make a U-turn at Tuas West Rd (signs for City/AYE/PIE/KJE) 83 m
3. Take the ramp onto Ayer Rajah Expy 1.9 km
4. Take the exit toward PIE/KJE 1.0 km
5. Merge onto Pan Island Expy/PIE 31.5 km
6. Take the exit toward Jalan Eunos 0.4 km
7. Turn right at Jalan Eunos 0.8 km
8. Slight left to stay on Jalan Eunos 38 m
9. Slight left at Sims Ave E 0.6 km
10. Turn right at Lorong Melayu 0.2 km
11. Turn right at Changi Rd 17 m
FROM AIRPORT
1. Head northeast on Airport Blvd 0.2 km
2. Slight right to merge onto T2 Blvd 0.2 km
3. Make a U-turn 0.4 km
4. T2 Blvd turns slightly left and becomes Airport Blvd 0.5 km
5. Continue on E Coast Pkwy 0.6 km
6. Merge onto Pan Island Expy/PIE via the ramp to TPE/SLE 9.9 km
7. Take the exit toward Jalan Eunos 0.4 km
8. Turn left at Jalan Eunos 0.6 km
9. Slight left to stay on Jalan Eunos 38 m
10. Slight left at Sims Ave E 0.6 km
11. Turn right at Lorong Melayu 0.2 km
12. Turn right at Changi Rd 17 m
FROM KEPPEL DISTRIPARK
1. Head southwest on Kampong Bahru Rd 0.3 km
2. Turn left to stay on Kampong Bahru Rd 0.5 km
3. Turn left at Keppel Rd 0.6 km
4. Take the ramp on the right to ECP 0.5 km
5. Merge onto ECP 9.9 km
6. Exit onto Still Rd S 2.1 km
7. Continue on Jalan Eunos 0.2 km
8. Turn right at Sims Ave E 0.6 km
9. Turn right at Lorong Melayu 0.2 km
10. Turn right at Changi Rd 17 m
FROM WOODLANDS
1. Head west on Woodlands Square toward S Woodlands Way 84 m
2. Slight left at S Woodlands Way 0.1 km
3. Turn left at Woodlands Avenue 5 0.3 km
4. Turn right at Woodlands Avenue 2 0.7 km
5. Take the ramp to SLE/CTE/TPE 0.5 km
6. Merge onto Seletar Expy/SLE 8.7 km
7. Take the exit on the right toward City 0.9 km
8. Merge onto Central ExpyPartial toll road6.7 km
9. Take the exit toward PIE 0.6 km
10. Merge onto Pan Island Expy/PIE 4.9 km
11. Take the exit toward Jalan Eunos 0.4 km
12. Turn right at Jalan Eunos 0.8 km
13. Slight left to stay on Jalan Eunos 38 m
14. Slight left at Sims Ave E 0.6 km
15. Turn right at Lorong Melayu 0.2 km
16. Turn right at Changi Rd 17 m
1. Head northwest on Jalan Ahmad Ibrahim toward Tuas West Rd 0.2 km
2. Make a U-turn at Tuas West Rd (signs for City/AYE/PIE/KJE) 83 m
3. Take the ramp onto Ayer Rajah Expy 1.9 km
4. Take the exit toward PIE/KJE 1.0 km
5. Merge onto Pan Island Expy/PIE 31.5 km
6. Take the exit toward Jalan Eunos 0.4 km
7. Turn right at Jalan Eunos 0.8 km
8. Slight left to stay on Jalan Eunos 38 m
9. Slight left at Sims Ave E 0.6 km
10. Turn right at Lorong Melayu 0.2 km
11. Turn right at Changi Rd 17 m
FROM AIRPORT
1. Head northeast on Airport Blvd 0.2 km
2. Slight right to merge onto T2 Blvd 0.2 km
3. Make a U-turn 0.4 km
4. T2 Blvd turns slightly left and becomes Airport Blvd 0.5 km
5. Continue on E Coast Pkwy 0.6 km
6. Merge onto Pan Island Expy/PIE via the ramp to TPE/SLE 9.9 km
7. Take the exit toward Jalan Eunos 0.4 km
8. Turn left at Jalan Eunos 0.6 km
9. Slight left to stay on Jalan Eunos 38 m
10. Slight left at Sims Ave E 0.6 km
11. Turn right at Lorong Melayu 0.2 km
12. Turn right at Changi Rd 17 m
FROM KEPPEL DISTRIPARK
1. Head southwest on Kampong Bahru Rd 0.3 km
2. Turn left to stay on Kampong Bahru Rd 0.5 km
3. Turn left at Keppel Rd 0.6 km
4. Take the ramp on the right to ECP 0.5 km
5. Merge onto ECP 9.9 km
6. Exit onto Still Rd S 2.1 km
7. Continue on Jalan Eunos 0.2 km
8. Turn right at Sims Ave E 0.6 km
9. Turn right at Lorong Melayu 0.2 km
10. Turn right at Changi Rd 17 m
FROM WOODLANDS
1. Head west on Woodlands Square toward S Woodlands Way 84 m
2. Slight left at S Woodlands Way 0.1 km
3. Turn left at Woodlands Avenue 5 0.3 km
4. Turn right at Woodlands Avenue 2 0.7 km
5. Take the ramp to SLE/CTE/TPE 0.5 km
6. Merge onto Seletar Expy/SLE 8.7 km
7. Take the exit on the right toward City 0.9 km
8. Merge onto Central ExpyPartial toll road6.7 km
9. Take the exit toward PIE 0.6 km
10. Merge onto Pan Island Expy/PIE 4.9 km
11. Take the exit toward Jalan Eunos 0.4 km
12. Turn right at Jalan Eunos 0.8 km
13. Slight left to stay on Jalan Eunos 38 m
14. Slight left at Sims Ave E 0.6 km
15. Turn right at Lorong Melayu 0.2 km
16. Turn right at Changi Rd 17 m
Control Valve that replaces a solenoid valve and a thermal expansion valve
A refrigeration system with electronic superheat control requires less mechanical components, because the electrical control valve combines the function of the expansion valve and the solenoid valve. The installation is much much easier because less mechanical components are used.
Wednesday, July 16, 2008
EX Series Heat Reclaim Control
R22 applications.
11kW --- EX6 heat reclaim control and EXD-U.. universal controller.
39kW --- EX7 heat reclaim control and EXD-U.. universal controller.
119kW --- EX8 heat reclaim control and EXD-U.. universal controller.
11kW --- EX6 heat reclaim control and EXD-U.. universal controller.
39kW --- EX7 heat reclaim control and EXD-U.. universal controller.
119kW --- EX8 heat reclaim control and EXD-U.. universal controller.
Tuesday, July 15, 2008
EX series Condensing Pressure and Liquid Regulator
R22, applications.
18kW --- EX5 Liquid mass flow control and EXD-U.. universal controller.
43kW --- EX6 Liquid mass flow control and EXD-U.. universal controller.
153kW --- EX7 Liquid mass flow control and EXD-U.. universal controller.
463kW --- EX8 Liquid mass flow control and EXD-U.. universal controller.
Monday, July 14, 2008
EX series Suction Pressure / Crankcase pressure regulator
Sunday, July 13, 2008
EX Series Hot gas bypass regulator components
R22, Minimum evaporating temperature -100 dec C.
4.9 kW EX4 capacity control and EXD-U.. univeral controller
16kW EX5 capacity control and EXD-U.. univeral controller
37kW EX6 capacity control and EXD-U.. univeral controller
131kW EX7 capacity control and EXD-U.. univeral controller
399kW EX8 capacity control and EXD-U.. univeral controller
Saturday, July 12, 2008
Electrical control valves and applicable controllers
Refrigeration, Air-Conditioning, Water Chillers.
Minimum evaporating temperature -100 deg C
2kW ....16.5kW for R22, EX4 expansion valve, EC3-X.. Superheat controller and EC3-3.. cold room controller.
5kW ....50kW for R22, EX5 expansion valve, EC3-X.. Superheat controller and EC3-3.. cold room controller.
15kW ....120kW for R22, EX6 expansion valve, EC3-X.. Superheat controller and EC3-3.. cold room controller.
Minimum evaporating temperature -50 deg C
35kW ....330kW for R22, EX7 expansion valve, EC3-X.. Superheat controller and EC3-3.. cold room controller.
90kW ....880kW for R22, EX8 expansion valve, EC3-X.. Superheat controller and EC3-3.. cold room controller.
Friday, July 11, 2008
Wednesday, July 09, 2008
Universal stepper motor control EXD-U
The universal stepper motor control EXD-U is used in all other commercial refrigeration and air-conditioning applications. Opening of the electrical control valve follows exactly the analog input signal of 0 ....10V or 4.... 20mA. The digital input signal is used to close the valve independently from analog input. When the digital signal switches the controller on again, the valve opens to the opening specified by the analog input. The optional selectable 'Start mode' first opens the valve 1/3 opening and then to the analog set point.
Tuesday, July 08, 2008
Advantages of EX Series Electrical Control Valves - Part 1
Valve seat and slider are made out of solid ceramic. Positive shut-off function eliminate the need for additional solenoid valve. The special form of the valve slide provides for proper floating through the valve and highly linear capacity characteristic between 10% and 100% of maximum capacity.
Download information
Download information
Monday, July 07, 2008
Superheat controller EC3-X33 with built-in backup battery and display unit ECD-002
The new electronic superheat controllers EC3-X33 control the superheat at the evaporator. A complete system consisting of electric control valve, superheat controller, temperature and pressure sensor controls the superheat exactly to set point, independent from condensing pressure. The MOP function protects the compressor from dangerous overload conditions. The positive shut-off function eliminates the use of an additional solenoid valve, because the built-in backup battery closes the valve after power is lost. The controller can be easily adjusted for each refrigerant and valve type.
Sunday, July 06, 2008
The Electronic Controllers from Emerson
The controller is responsible for the various control tasks. Emerson controllers are optimized for the requirements of refrigeration and air-conditioning and perform all control tasks which have been performed by conventional valves in the past, as superheat control or capacity control.
Wednesday, July 02, 2008
How energy is saved by applying electrical control valves?
The recent energy price increases caused an explosion in the system operating cost. Reducing energy consumption saves money and as a beautiful side effect protects the environment.
Refrigeration and air-conditioning systems belong to the big energy consumers all over the world. Means to reduce the energy consumption have a strong effect on the cost.
Under full load conditions or fixed condensing pressure, conventional, as well as electronic systems operate efficiently. Under partial load or floating condensing pressure, which happens at low ambient temperature (e.g. at cloudly weather, at night, in spring, fall or winter) the condensing pressure decreases. In this case, thermal expansion valves tend to oscillate, which decreases their lifetime. Systems with electronic valves and controllers operate in partial load in the same exact and stable manner as under load. This potential to save energy is best at low condensing pressure.
Under full load conditions or fixed condensing pressure, conventional, as well as electronic systems operate efficiently. Under partial load or floating condensing pressure, which happens at low ambient temperature (e.g. at cloudly weather, at night, in spring, fall or winter) the condensing pressure decreases. In this case, thermal expansion valves tend to oscillate, which decreases their lifetime. Systems with electronic valves and controllers operate in partial load in the same exact and stable manner as under load. This potential to save energy is best at low condensing pressure.
Tuesday, June 24, 2008
Latest Version of Catalogues
As our products in stock have undergone revisions and upgrades. We advice customers to refer to the latest versions of our catalogs. They can be downloaded from our website. If you are unsure of the differences, please check with us, your local wholesaler. Thank you.
Wednesday, June 04, 2008
Take Apart Liquid Line Filter Drier - 2-5/8" ODF Connection
For 101 tons ~ R-134a or 107 tons ~ R407C applications.
At 30 deg C liquid refrigerant temperature.
Selection: PCN 037570, ADKS 400 21 T.
Maximum working pressure: 500psig
Filtration: 40 micron, with H100 blocks.
At 30 deg C liquid refrigerant temperature.
Selection: PCN 037570, ADKS 400 21 T.
Maximum working pressure: 500psig
Filtration: 40 micron, with H100 blocks.
Monday, June 02, 2008
Troubleshooting EPRBS Regulators
Problem A:
EPRBS regulator will not open.
Causes:
1) Excess dirt in pilot/ solenoid.
2) Piston bleed hole restriction.
3) Coil is damaged or not energized.
Corrective Action:
Disassemble valve and clean. Replace if necessary.
Verify coil is energized. Replaced if necessary.
EPRBS regulator will not open.
Causes:
1) Excess dirt in pilot/ solenoid.
2) Piston bleed hole restriction.
3) Coil is damaged or not energized.
Corrective Action:
Disassemble valve and clean. Replace if necessary.
Verify coil is energized. Replaced if necessary.
Wednesday, April 30, 2008
Friday, April 18, 2008
Wednesday, March 19, 2008
Thermal Expansion Valve for Ultra Low Temperatures
This is designed for ultra low temperature applications such as environmental test chambers and other applications where the desired evaporator temperature is below -40C [-40F].
Maximum working pressure: 450psig.
Tuesday, March 04, 2008
Tuesday, February 26, 2008
Monday, February 25, 2008
ARI 710-2004: Performance Rating of Liquid-Line Driers
Source: Air-Conditioning and Refrigeration Institute
Scope
This standard establishes a single set of requirements for the testing and rating of water capacity and refrigerant flow capacity for driers to be used in the liquid lines of refrigerating and air-conditioning systems; whereby, equipment performance can be compared from product to product.
Download
Scope
This standard establishes a single set of requirements for the testing and rating of water capacity and refrigerant flow capacity for driers to be used in the liquid lines of refrigerating and air-conditioning systems; whereby, equipment performance can be compared from product to product.
Download
Friday, January 18, 2008
Electrical Control Valves
Improved energy efficiency, tighter temperature controls, wider range of operating conditions, remote monitoring and diagnostics functions.
Check with your local wholesaler for details.
Friday, January 11, 2008
200 Series Solenoid Valve
R12 Liquid line application 8.7kW - 97.6kW
R134A Liquid line application 10.4kW - 117.5kW
R22 Liquid line application 11.0kW - 124.0 kW
R407C Liquid line application 10.3kW - 128.0kW
R404A/507 Liquid line application 7.4kW - 81.4 kW
R502 Liquid line application 7.1kW - 80.4kW
For other applications, capacities and performance information, please seek advice from your local wholesaler.
240 Series Solenoid Valve
R134A Liquid line application 52.5kW - 307.4kW
R22 Liquid line application 55.2kW - 338.0 kW
R407C Liquid line application 52.4kW - 321.0kW
R404A Liquid line application 36.5kW - 230.0 kW
For other applications, capacities and performance information, please seek advice from your local wholesaler.
Subscribe to:
Posts (Atom)